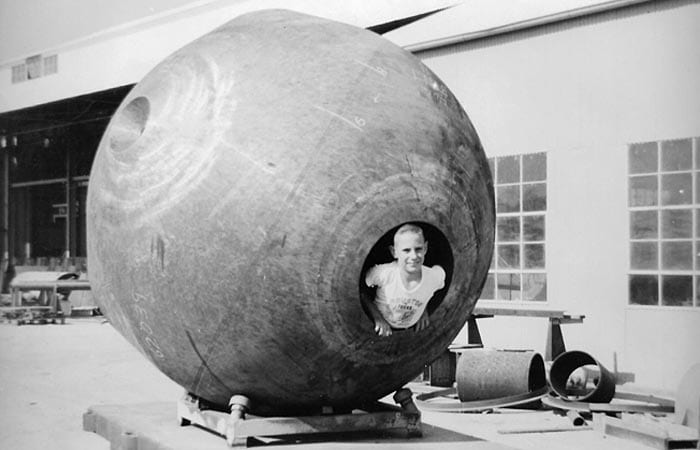
The Boy in the Alvin Sphere
Testing the sub's personnel sphere—then and now
The titanium personnel sphere for the new deeper-diving Alvin submersible began undergoing a series of tests Tuesday in a pressurized tank at a facility in Annapolis, Md., to see how it reacts to pressures simulating depths from 6,500 to 8,000 meters (4 to 5 miles). It seemed a perfect time to publish this gem of an e-mail and photographs, which we received from the son of the engineer who built Alvin’s original pressure hull, a pressure-resistant sphere, made of steel, that housed scientists and pilots during dives.
To the Editor:
Thank you for writing the story of the deep submersible Alvin on the Woods Hole Oceanographic Institution website. My name is Raymond Pechacek Jr., and I thought you might be interested in some additional details concerning Alvin’s early history.
My father, Raymond Pechacek Sr., was vice president for engineering at Hahn and Clay in Houston, Texas, and personally designed the original pressure hull for Alvin. My Dad talked quite a bit about designing and building Alvin, and it was an important part of his career. He passed away on Jan. 31, 1999.
I ‘interviewed’ him concerning his design work on Alvin around Christmas shortly before he died. I heard bits and pieces of the account throughout my life and wanted to learn the full version.
My Dad said Alvin’s pressure hull was the heart of the sub design—the stronger the hull, the deeper Alvin could dive. The objective was to design, develop, and build as perfectly round a sphere as possible, so the extreme pressure of the ocean would be equally distributed on all surfaces.
He explained that existing technology allowed Hahn and Clay machinists to fabricate the two perfectly formed sphere halves he designed to withstand the extreme deep ocean pressure. However, the challenge was how to join the two halves together. Standard room-temperature welding practices of the day would create a weak link when joining the hull seam, and Alvin could fail at far less depth than the desired requirement.
My Dad pondered this dilemma in great detail, since it was the core of the entire design and success (or failure) for Alvin. He knew he could not follow standard practices. So after much thought, he invented a unique manufacturing process to solve the problem.
He directed Hahn and Clay fabricators to heat the two pressure vessel halves evenly by rotating them on a rig around torches. This action caused all surfaces to expand evenly. Upon reaching the desired temperature, the two sides were connected, and the seam welded.
Most important, as the two halves cooled, the weld also cooled, contracted, and completely integrated with the rest of the pressure hull, forming a perfect, seamless sphere.
Pressure testing exceeded all expectations. After the sphere went far beyond the original requirements, they tried to destroy it to learn its limitations, but the test chamber was unable to develop enough pressure to affect it. Alvin went into service, and the rest is history.
I had the privilege of ‘hanging out’ at Hahn and Clay many times when I was a kid and also worked in the factory during summer breaks from college. I remember seeing the heating process for Alvin when my Dad took me to the shop one evening. Obviously he was very concerned about every aspect of Alvin’s building process.
One of my most prized mementos is the picture taken of me in Alvin. And my Dad had Bill Rainnie, Alvin’s senior pilot, personally sign it for me! My family and I followed Alvin’s amazing exploits through the years (and still do).
Best regards,
Raymond Pechacek, Jr.
Wentzville, Mo.
Rainnie inscribed the photo: “To Raymond: With best wishes for success as an engineer—when the time comes. W.O. Rainnie, Sr. Pilot Alvin.”
***
In a subsequent e-mail, Mr. Pechacek wrote that his father “was always amazed that a cereal company (General Mills) was the prime contractor for Alvin.”
He told me the Navy and other ‘conventional’ contractors were not able to develop a design for the pressure vessel that would meet the depth requirement specifications—too much risk. So General Mills accepted the bid.
I am not sure if General Mills accepted the bid after talking to Hahn and Clay. My Dad told me (once again, hearsay) that General Mills negotiated the subcontract with Henry Clay, Hahn and Clay’s owner at the time.
General Mills asked Henry for a performance clause to mitigate its risk. They requested Hahn and Clay pay “X” amount of money in penalties for each “Y” amount of depth if the pressure vessel failed before meeting the depth specs. Henry thought about it and countered General Mills should pay Hahn and Clay a bonus for each “Y” amount of depth if the vessel exceeded the depth requirement. Apparently this was a novel feature for contracts of the day. I understand General Mills did not like it but ultimately accepted it. My Dad said Henry made some good money on the contract when the test chamber failed before the pressure vessel did.
I did find the attached photo of my father in the room at Hahn and Clay where Alvin was designed (basically a large loft above the factory floor where all the engineers worked together). The picture is not dated but was taken close to Alvin‘s design date. It may be interesting from a historical perspective due to the technology available in the late fifties and early sixties (plus the clothes style engineers wore to work every day at the time—sleeves rolled up and ready for work).
I used to play with the adding machine in the background when my Dad took me to work on some Saturday mornings. He also let me make copies of blueprints using an incredibly large machine that used smelly chemicals. I’m pretty sure it would not pass OSHA requirements today. The phones were still rotary dial, and there was no such thing as an area code. I still remember my Dad’s phone number: OR 2-1671. It is amazing such complex and successful engineering designs such as Alvin were done completely on a slide ruler and typewriter-size adding machines. …
***
Mr. Pechacek Sr. went on to work on other important projects, including the space shuttle. Mr. Pechacek Jr. became a project manager, specializing in supply chain, transportation, and global trade management operations, “but I have worked with many engineers!” he wrote.
Bill Rainnie, an oceanographic engineer and research specialist, was recruited in 1961 by WHOI scientist Allyn Vine (after whom Alvin is named). He headed the program to build Alvin, participating in the design, construction, testing, and operation of Alvin as well as the support ship, Lulu. He was the first qualified pilot and took the first manned test dives in 1964. He directed Alvin operations in 1966 to search for and recover an H-bomb that fell into the sea off Palomares, Spain, in 1966. In 1968, Alvin’s cradle support cables failed and Alvin slid into the water and sank to the bottom in 5,000 feet of water. Rainnie convinced the Navy that Alvin should be recovered, and he led operations to recover, refurbish, and return the sub to service for science in 1969. In all, Rainnie conducted 80 dives as pilot-in-command and about 220 dives as expedition leader/operations from 1966 to 1973. He was awarded commendation citations and Navy meritorious public service awards for his leadership and efforts in deep submergence. He died in 1985.
In 2009, engineers began building a new personnel sphere for Alvin that will extend its depth capacity from 4,500 meters, or 2.8 miles, to 6,500 meters, or more than 4 miles. That will also extend Alvin’s reach, allowing it to explore 98 percent of the seafloor, up from its previous limit of 63 percent.
On June 11, 2012, the new sphere was shipped from the Southwest Research Institute, in San Antonio, Texas, to a Northrop Grumman facility in Annapolis, Md., for tests to verify that the design, material, and fabrication meet requirements for safe operation of the sub. Sensors on the sphere will gauge its response to pressures simulating depths of 6,500 meters. To build in a safety factor, one test dive will put the sphere under pressure of 12,000 pounds per square inch, simulating a depth of about 8,000 meters, or 5 miles.
If all goes according to plan, the new sphere will be transported to WHOI, arriving sometime during the first week of July. There, engineers will reassemble the newest incarnation of Alvin. It will have five viewports, compared with the three that previous Alvins had. Can’t you just picture a photograph with a lucky kid’s head poking out of one of them?
Slideshow
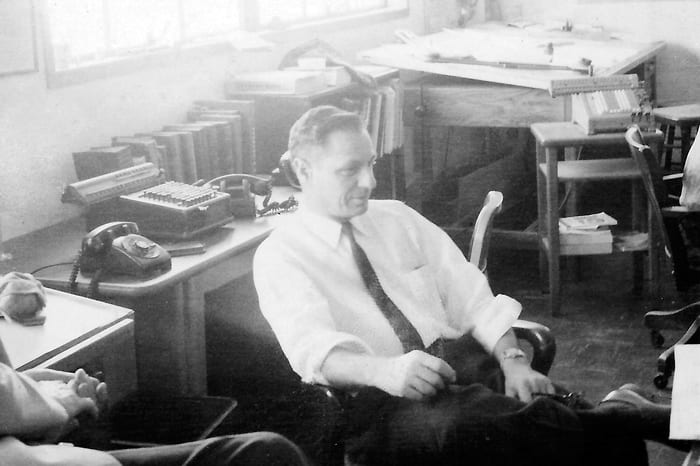
Slideshow
- Raymond Pechacek Sr. sits in his office at Hahn and Clay in Houston, Texas, around the time he supervised construction of the original Alvin personnel sphere in the early 1960s. (Courtesy of Raymond Pechacek Jr.)
- Alvin pilot Bill Rainnie (left) and Earl Hays, first chairman of the WHOI Department of Applied Oceanography, test the deep submergence research vehicle Alvin in 1964. They were key figures involved in the design, construction, testing, and utilization of Alvin. (WHOI Archives)
- Two hemispheres of titanium were forged in a plant in Wisconsin to create Alvin's new personnel sphere. Subsequently, engineers in California and Texas removed material from the hemishphere's interiors and exteriors to reduce its thickness to 3 inches. The sphere will be pressure tested next week in Anapolis, Md., before its scheduled arrivat at WHOI in July. (Photo courtesy of the Advanced Imaging & Visualization Laboratory, Woods Hole Oceanographic Institution)
- A preliminary view of the "new" Alvin, which will be assembled at WHOI starting in the summer of 2012. (Illustration by Megan Carroll, Woods Hole Oceanographic Institution)
- The new titanium personnel sphere for Alvin is set for loading into the chamber of a massive pressure-testing instrument at a Northrop Grumman facility in Annapolis, Md. The ram-like instrument at right seals the chamber, in which pressures will be increased to those simulating depths of 6,500 meters (the depth to which the sub will go) and higher. (Bruce Strickrott, Woods Hole Oceanographic Institution)
- Sensors on the sphere will gauge the sphere's response to pressures simulating depths of 6,500 meters and higher to verify that the design, material, and fabrication meet requirements for safe operation of the sub. (Courtesy of Kurt Uetz, Woods Hole Oceanographic Institution)
Related Articles
Featured Researchers
See Also
- Building the Next-Generation Alvin Submersible from Oceanus magazine
- Alvin Gets an Interior Re-design from Oceanus magazine
- The Human-Occupied Vehicle Alvin
- History of Alvin
- Alvin's Pilots from Oceanus magazine
- National Deep Submergence Facility