Meet the Alvin 6500 Team: Francis Elder
Lead Mechanical Engineer Francis Elder helps re-draw Alvin’s future
By Hannah Piecuch | December 17, 2020
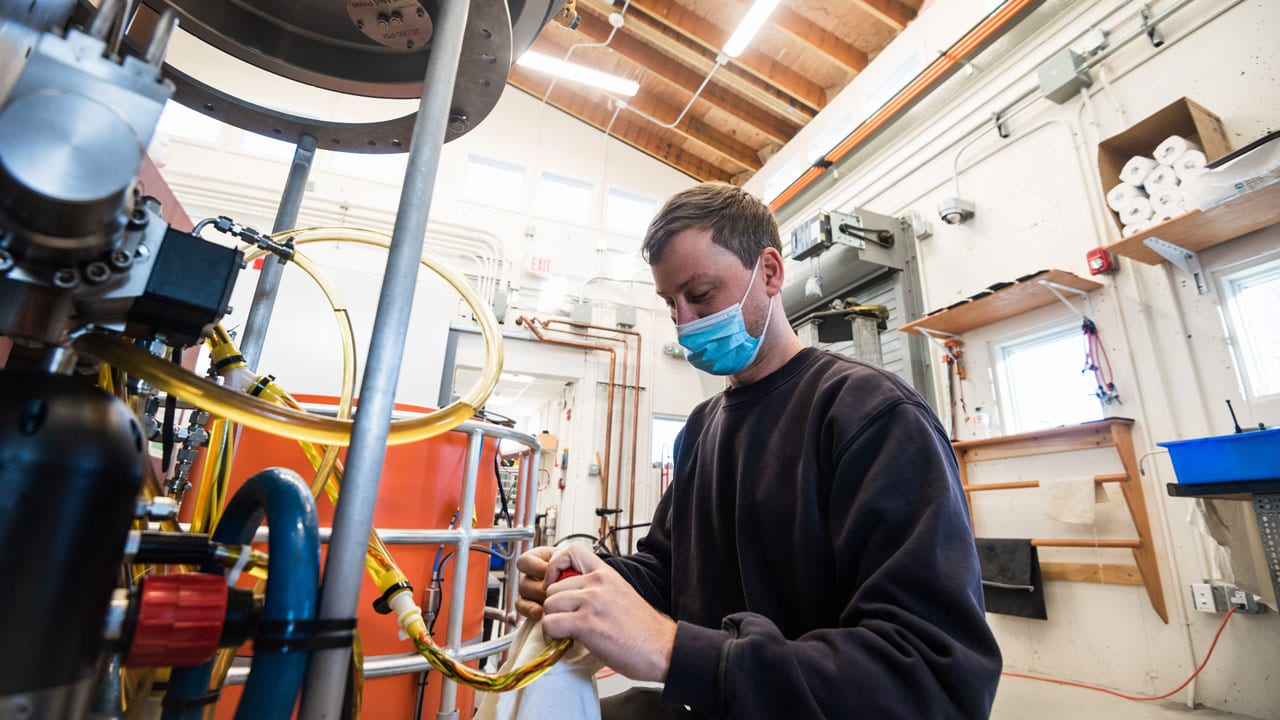
In early 2020, when the COVID-19 pandemic was still in its initial phases, the deep-submergence vehicle Alvin returned to Woods Hole for one of its regular, five-year overhauls. But this one is slightly different. Instead of taking the sub apart, inspecting every part, and putting it back together again, the Alvin Group is entirely revamping the sub. When complete next summer, the sub will be capable of diving to 6,500 meters–2,000 meters deeper than it is currently capable. The overhaul is also an opportunity to rebuild and redesign critical systems.
Francis Elder is the lead mechanical engineer for the Alvin Group. When Alvin is at sea, his work involves maintaining and updating the sub to support regular operations, as well as system-level design for other vehicle groups and labs within the Institution. He took some time to speak about his work on Alvin.
This is the first interview in a multi-part series with members of the Alvin Group.
Oceanus: You have been working for the Alvin group since the end of its last overhaul in 2012. What brought you to WHOI?
Fran: I grew up here in Falmouth and went to Wentworth for college. I got a co-op internship at WHOI doing instrument design and working on Arctic winches. It was a fun group to be in. I learned a lot from the people I worked under. When I was graduating, that group didn’t have a position for me, but I had done work for the Alvin Group and they hired me on to do document management for the last overhaul. Then the project manager asked if I could design an electronics chassis. I was like, “Yep, I definitely can do that.” And I just went from there. I kept saying, “Yes, I can do that.”
Oceanus: Now you’re the lead mechanical engineer and your team is in the midst of another overhaul. What types of things are you working on?
Fran: I am responsible for all mechanical aspects of upgrading the submersible including the general arrangement of weight and balance, the new frame, new syntactic foam, changes to the ballast systems, new thrusters, new hydraulic system, and more. There are a lot of systems being upgraded, but the highlight of this whole upgrade for me is the variable ballast system. That definitely has the most tentacles.
Oceanus: What does the variable ballast system do?
Fran: It’s a series of titanium spheres that can hold water and air to help the sub achieve neutral buoyancy underwater. When we go to depth, we drop some of the weights that brought Alvin down. We want to be neutral so we don’t have to use our thrusters to maintain position vertically in the water. So we pump water in or out of the system to achieve neutral buoyancy. Alvin is a battery-powered vehicle, so we want to be as efficient as possible.
The new system has to be able to withstand the higher pressures at 6,500 meters operating depth, so it needed thicker-walled spheres, thicker-walled plumbing, new valves, and a new high-pressure pump.
Oceanus: What part of the ballast system are you working on now?
Fran: I am designing a new pump, which is sort of the heart of the system. It’s the main pump for pumping seawater in and out. The current one is a very impressive thing but it is complex, expensive, and didn’t meet our needs for this overhaul. So we switched to a hydraulicly powered intensifier pump.
We found an off-the-shelf pump that’s commercially available, but it kept breaking every time we tested it. We went through multiple iterations with them and finally it made sense to just do it ourselves. We paid for the drawings, then I modeled all the drawings and made all the tweaks. We redesigned the check valves and changed all the materials. These are complex parts, with lots of machining operations and crazy materials. They are titanium and have high-pressure seals and bearings, and it’s all made to very tight tolerances.
Now that we’ve settled on a design, we’re torture testing it, trying to find out how long until this thing breaks, so we know how long we can use it before we need to service it. It’s up at the pressure test facility at 10,000 PSI, basically pressure testing itself. The plan after that is to hang it off the dock and let it go for a long time in salt water.
Francis Elder loads the new variable ballast pump into the chamber at WHOI's pressure test facility. (© Daniel Hentz Photography)
Oceanus: What is one of the biggest challenges of getting Alvin to these extreme depths?
Fran: I don’t think it is going to be too hard to get down to 6,500 meters. The real test is when Alvin goes to work. What makes Alvin different is that it is not just about going there. It’s got to work and it’s got to work hard for a long time in a really harsh environment. This is a reality of working in the ocean. But Alvin also has to work reliably all year long without getting serviced. This is no easy task, and the real challenge will be making it work every day until the next overhaul.
Oceanus: What is one thing that you wish the public knew about Alvin?
Fran: People have this conception that the sub is antiquated in some way—but it’s not. We are continually applying new technology to how Alvin runs. It’s been 50 years of tweaking, and that’s what makes the sub so reliable.